The construction of the New Bauhaus Museum is a project by the Klassik Stiftung Weimar. The planned museum will be built near the Weimarhallenpark and will present the Weimar collections of the State Bauhaus, which was founded in Weimar in 1919. The museum is scheduled to open in 2015.
The Gropius Collection, owned by the Klassik Stiftung Weimar, is the world’s oldest collection of original Bauhaus works. The collection was significantly expanded with the acquisition of the Ludewig Collection in 2010, which contained 1,500 objects of functional design dating from 1780 to the present, including important Bauhaus works. Aside from the Bauhaus Archive in Berlin, the Bauhaus collection in Weimar is unarguably one of the world’s most important in terms of size and quality.
Awards:
A total of €169,000.00 has been set aside for prizes, allotted as follows (all prizes incl. value-added tax; net
sums in parenthesis):
1st prize €55,000.00 (€46,218.49)
2nd prize €45,000.00 (€37,815.13)
3rd prize €32,500.00 (€27,310.92)
4th prize €20,000.00 (€16,806.72)
5th prize €10,000.00 (€8,403.36)
For commendations: a total of €6,500.00 (€5,462.18)
Budget:
The funding body provided the following budget for the construction of Weimar’s new Bauhaus museum:
cost of construction alone = sum for building (cost groups 300 + 400): €14.500,00 gross.
Design Challenge:
Weimar owns a unique collection on the background, history and after-effects of “Staatliches Bauhaus“, which was founded there in 1919. In 1995 a temporary Bauhaus museum was set up. Thanks to a special funding programme run by the German government and the state of Thuringia, the Klassik Stiftung Weimar foundation was able to set up a new Bauhaus museum in Weimar. This project is part of the ‘Kosmos Weimar‘ master plan, which covers all the foundation’s facilities, giving Weimar the opportunity to set a succinct example in terms of architecture and urban development.
The purpose of the competition was to find the best solution both for the new Bauhaus museum itself and for the location’s urban development potential. The competition was to be split in two parts – he first stage of the competition was the development of a fundamental design concept, selecting a suitable location and tackling the open spaces surrounding it in the context of urban planning. Furthermore, the urban design concept in Stage 1 is to plan for a possible future museum extension and a kindergarten.
In the second stage of the competition the focus is on working in greater detail on the architectural and interior concept of the new museum building. The solution to the task is expected to fit in with urban planning, be architecturally innovative and sustainable, save energy and stand up to museological requirements.
On 16. March 2012 the international jury awarded two second-place and two third-place prizes and conferred three honourable mentions.
The design proposal for the New Bauhaus Museum by Pedro Monteiro, Rodrigo Cruz, and Sérgio Silva establishes a volumetric relation with the Gauforum in regard to its location. The first thing you see is a tower of light. It leads the way. As you walk along the narrow line of Oskar Schlemmer’s logo, you are entering Bauhaus. As it gains depth, the two-dimensional design of the logo becomes a geometrical stone sculpture. Its occupation defines its architecture.
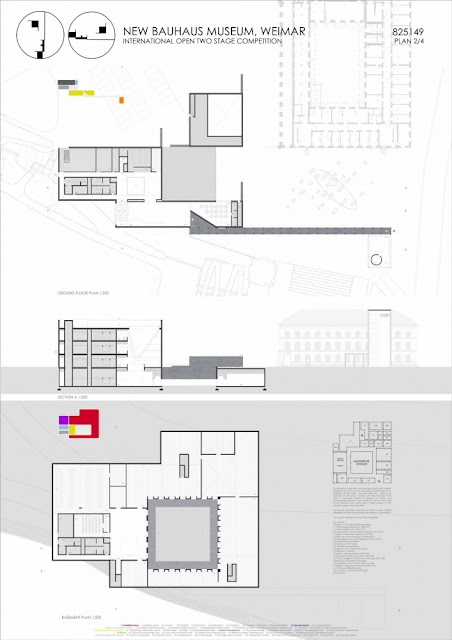
A first building, made of glass and steel, marks the beginning of the access route to the museum while a stone pathway leads to the museum entrance and the ground floor. This is where the social areas – foyer and café – are located The exhibition areas and the cinema are located in the underground floor, as well as a viewable depot for items from the Weimar Bauhaus collection. The depot’s location allows it to be a part of the exhibition, as well as to be used independently.
The exhibition areas are organized around a courtyard that may be used as an outside exhibition area, or as a venue for other events (Bauhaus Theatre, larger conferences, etc.). The floors above include the spaces where the access is more exclusive: the pedagogical areas on the first floor and the offices on the second floor.
The location of the exhibition areas under the ground is a consequence of the necessity to control their environment as much as possible. Since the terrain remains stable, those areas benefit from geothermal mass to reduce the need for insulation and mechanical control of the temperature. The courtyard organization, as a cloister, guarantees the natural circulation of air in those areas. The ventilated facade in stone assures that the rest of the building, where the environment conditions are not as demanding, is properly insulated and ventilated, reducing energy other expenditures.
The announcement of the winners officially concluded the architectural design competition. The two second-place prizes went to Johann Bierkandt (Landau) and the Architekten HKR (Klaus Krauss and Rolf Kursawe, Cologne).
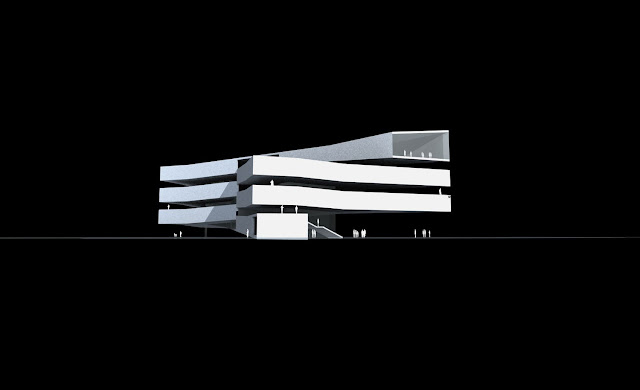
The two third-place prizes went to Prof. Heike Hanada with Prof. Benedict Tonon (Berlin) and Bube/Daniela Bergmann (Rotterdam).
Three honourable mentions were awarded to the proposals by Karl Hufnagel Architekten (Berlin), hks Hestermann Rommel Architekten und Gesamtplaner GmbH (Erfurt), and menomenopiu architectures/Alessandro Balducci (Rome).
The Klassik Stiftung Weimar will now begin negotiating with the four prize winners according to VOF procedure (Contracting Regulations for the Awarding of Professional Services). The jury provided the winners with recommendations for optimising their proposals in preparation for the VOF procedure.
All proposals of the second round of the competition are displayed at the Neues Museum in Weimar.